Comparison of different sintering methods of ZrC (zirconium carbide) ceramics and analysis of their application performance
ZrC( zirconium carbide) ceramic materials have high melting point, low density and wear resistance. Excellent temperature resistance and oxidation and ablation resistance, it can be used in the service environment of hypersonic aircraft nose cones, wing leading edges and aviation ramjet nozzles. It can be regarded as one of the candidate materials for the extreme thermal components of hypersonic aircraft and has received widespread attention .At present, the research on ZrC ceramic materials mainly focuses on improving the sintering performance of ZrC ceramic materials, low-temperature oxidation resistance and improving the fracture toughness of the materials.
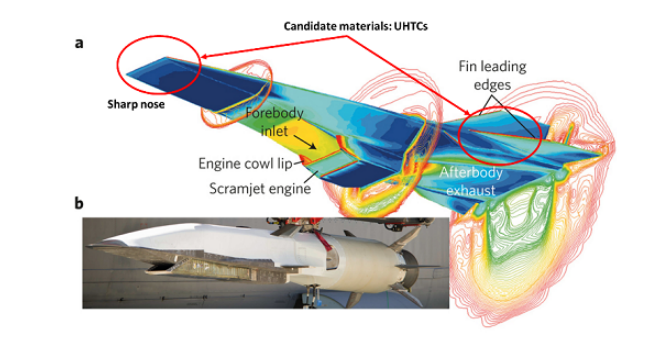
1. Sintering performance of ZrC ceramic materials
Due to the extremely high melting point of ZrC ceramic material, in order to achieve sintering and densification of the material, it is generally necessary to perform the sintering temperature (≥1800°C) and pressure (˃20MPa), that is, the hot pressing sintering process. At the same time, some scholars use pressureless sintering, reactive hot pressing sintering and spark plasma sintering technology to achieve the densification of ZrC ceramic materials.
1.1 Hot pressing sintering
At present, hot-pressing (HP) is the most widely used method of sintering and densification of ZrC-based ultra-high temperature ceramic materials. Hot-press sintering can densify the sintered body by changing the sintering temperature under a certain pressure condition, and can also make the green body sintered and densified by adjusting the external pressure under a certain sintering temperature.
Advantages:
(1) The required forming pressure is only 1/10 of the cold pressing method;
(2) Reduce the sintering temperature and shorten the sintering time, and inhibit the growth of crystal grains
Disadvantages:
(1) Hot-pressed and sintered materials are anisotropic, and the material properties of parallel hot-pressed and vertical hot-pressed directions are very different;
(2) The hot-pressed sintered material has a single geometric shape and a small size;
(3) Hot-pressed sintered materials need to be processed with high cost, long time and complicated process.
1.2 Pressureless sintering
Compared with traditional hot-press sintering to prepare ultra-high temperature ceramic materials, its pressureless sintering process has many excellent characteristics. Because it does not require additional external force during the sintering process, it can achieve more complex ultra-high temperature The ceramic material is formed without defects, and the ceramic green body is sintered and densified. Usually the pressureless sintering of ultra-high temperature ceramic materials is combined with the corresponding green body preparation process, such as gel injection molding of ultra-high temperature ceramic powder, pressureless sintering after drying and debinding, or cold isostatic processing of ceramic powder After pressing, pressureless sintering is performed to obtain a dense and uniform ultra-high temperature ceramic sintered body.
Advantages:
(1) The near-net shape of ceramic materials can be achieved without additional processing;
(2) The prepared ceramic material has isotropic characteristics, so the performance is stable
Disadvantages:
(1) It is usually necessary to introduce sintering aids for sintering densification
(2) The pressureless sintering temperature is relatively high and the cost is relatively high.
1.3 Reaction hot pressing sintering
Reactive hot-pressing (RHP) preparation of ultra-high temperature ceramic materials includes two stages: in-situ reaction of ceramic powder and hot-pressing sintering densification. Its biggest advantage lies in the direct in-situ synthesis of ultra-high temperature ceramic powder, and the synthesized powder can ensure uniform mixing, which avoids the need for long-term mechanical mixing of ZrC ceramic powder in the traditional sintering process. The reactive hot pressing sintering directly performs hot pressing sintering of the ZrC ceramic powder synthesized in situ, which shortens the preparation cycle and has high production efficiency.
1.4 Spark plasma sintering
The principle of spark plasma sintering (Spark Plasma Sintering, SPS) to prepare ZrC ceramic materials is: a powerful pulsed DC voltage is generated by a dedicated motor. When the pulsed voltage is transferred to the ZrC ceramic powder, a discharge plasma will be generated in the gap of the ZrC powder. The body is further sintered and densified by ZrC powder, thereby obtaining a uniform and dense ZrC ceramic material.
2. Oxidation resistance of ZrC ceramic materials
The poor low-temperature oxidation resistance of carbide ceramics is mainly due to the low initial oxidation temperature of carbide ceramics (for example, the initial oxidation temperature of ZrC is 450°C), and the melting point of its oxidation products is too high, and the temperature is relatively low (<1900< span="">℃) It is a powdery solid, which cannot prevent the oxygen from corroding the inside of the material. At present, there is no good solution to the low temperature and easy oxidation of ZrC ceramics, and it can only be alleviated to a certain extent by introducing additives.
However, ZrC ceramic materials have excellent oxidation and ablation resistance in high temperature environments. This is mainly due to the fact that ZrC ceramics can form high-viscosity glass oxides ZrO2 under ultra-high temperature and oxidizing environments. These glassy substances cover the material. The surface can block oxygen from entering the inside of the material, thereby protecting the inner layer material.
3. Fracture toughness of ZrC ceramic materials
For a long time, ultra-high temperature resistant ceramic materials and their components are mainly prepared by sintering process. The resulting ceramics have low fracture toughness (generally around 2~4MPa·m1/2), poor thermal shock resistance, and are prone to occur during rapid heating. Damage, causing catastrophic failure. Therefore, improving the brittleness of ZrC ceramic materials is the research focus of later materials workers.
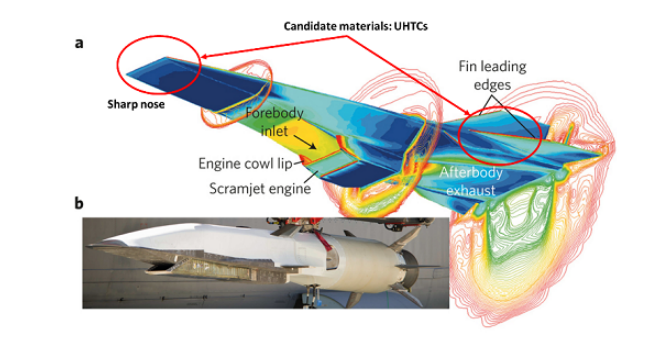
1. Sintering performance of ZrC ceramic materials
Due to the extremely high melting point of ZrC ceramic material, in order to achieve sintering and densification of the material, it is generally necessary to perform the sintering temperature (≥1800°C) and pressure (˃20MPa), that is, the hot pressing sintering process. At the same time, some scholars use pressureless sintering, reactive hot pressing sintering and spark plasma sintering technology to achieve the densification of ZrC ceramic materials.
1.1 Hot pressing sintering
At present, hot-pressing (HP) is the most widely used method of sintering and densification of ZrC-based ultra-high temperature ceramic materials. Hot-press sintering can densify the sintered body by changing the sintering temperature under a certain pressure condition, and can also make the green body sintered and densified by adjusting the external pressure under a certain sintering temperature.
Advantages:
(1) The required forming pressure is only 1/10 of the cold pressing method;
(2) Reduce the sintering temperature and shorten the sintering time, and inhibit the growth of crystal grains
Disadvantages:
(1) Hot-pressed and sintered materials are anisotropic, and the material properties of parallel hot-pressed and vertical hot-pressed directions are very different;
(2) The hot-pressed sintered material has a single geometric shape and a small size;
(3) Hot-pressed sintered materials need to be processed with high cost, long time and complicated process.
1.2 Pressureless sintering
Compared with traditional hot-press sintering to prepare ultra-high temperature ceramic materials, its pressureless sintering process has many excellent characteristics. Because it does not require additional external force during the sintering process, it can achieve more complex ultra-high temperature The ceramic material is formed without defects, and the ceramic green body is sintered and densified. Usually the pressureless sintering of ultra-high temperature ceramic materials is combined with the corresponding green body preparation process, such as gel injection molding of ultra-high temperature ceramic powder, pressureless sintering after drying and debinding, or cold isostatic processing of ceramic powder After pressing, pressureless sintering is performed to obtain a dense and uniform ultra-high temperature ceramic sintered body.
Advantages:
(1) The near-net shape of ceramic materials can be achieved without additional processing;
(2) The prepared ceramic material has isotropic characteristics, so the performance is stable
Disadvantages:
(1) It is usually necessary to introduce sintering aids for sintering densification
(2) The pressureless sintering temperature is relatively high and the cost is relatively high.
1.3 Reaction hot pressing sintering
Reactive hot-pressing (RHP) preparation of ultra-high temperature ceramic materials includes two stages: in-situ reaction of ceramic powder and hot-pressing sintering densification. Its biggest advantage lies in the direct in-situ synthesis of ultra-high temperature ceramic powder, and the synthesized powder can ensure uniform mixing, which avoids the need for long-term mechanical mixing of ZrC ceramic powder in the traditional sintering process. The reactive hot pressing sintering directly performs hot pressing sintering of the ZrC ceramic powder synthesized in situ, which shortens the preparation cycle and has high production efficiency.
1.4 Spark plasma sintering
The principle of spark plasma sintering (Spark Plasma Sintering, SPS) to prepare ZrC ceramic materials is: a powerful pulsed DC voltage is generated by a dedicated motor. When the pulsed voltage is transferred to the ZrC ceramic powder, a discharge plasma will be generated in the gap of the ZrC powder. The body is further sintered and densified by ZrC powder, thereby obtaining a uniform and dense ZrC ceramic material.
2. Oxidation resistance of ZrC ceramic materials
The poor low-temperature oxidation resistance of carbide ceramics is mainly due to the low initial oxidation temperature of carbide ceramics (for example, the initial oxidation temperature of ZrC is 450°C), and the melting point of its oxidation products is too high, and the temperature is relatively low (<1900< span="">℃) It is a powdery solid, which cannot prevent the oxygen from corroding the inside of the material. At present, there is no good solution to the low temperature and easy oxidation of ZrC ceramics, and it can only be alleviated to a certain extent by introducing additives.
However, ZrC ceramic materials have excellent oxidation and ablation resistance in high temperature environments. This is mainly due to the fact that ZrC ceramics can form high-viscosity glass oxides ZrO2 under ultra-high temperature and oxidizing environments. These glassy substances cover the material. The surface can block oxygen from entering the inside of the material, thereby protecting the inner layer material.
3. Fracture toughness of ZrC ceramic materials
For a long time, ultra-high temperature resistant ceramic materials and their components are mainly prepared by sintering process. The resulting ceramics have low fracture toughness (generally around 2~4MPa·m1/2), poor thermal shock resistance, and are prone to occur during rapid heating. Damage, causing catastrophic failure. Therefore, improving the brittleness of ZrC ceramic materials is the research focus of later materials workers.
related news
-
Nov 03, 2022application of zirconium carbide powder
-
Jan 17, 2022Laser Cladding Metal-Based Titanium Carbide Strengthening Coating
-
Dec 13, 2021Effect of Mo–Si–B on Sintering Process and Properties of ZrB2 Ultra-high-Temperature Ceramics
-
Dec 21, 2021Strengthening and Toughening of Zirconium Diboride Ultra-High Temperature Ceramics